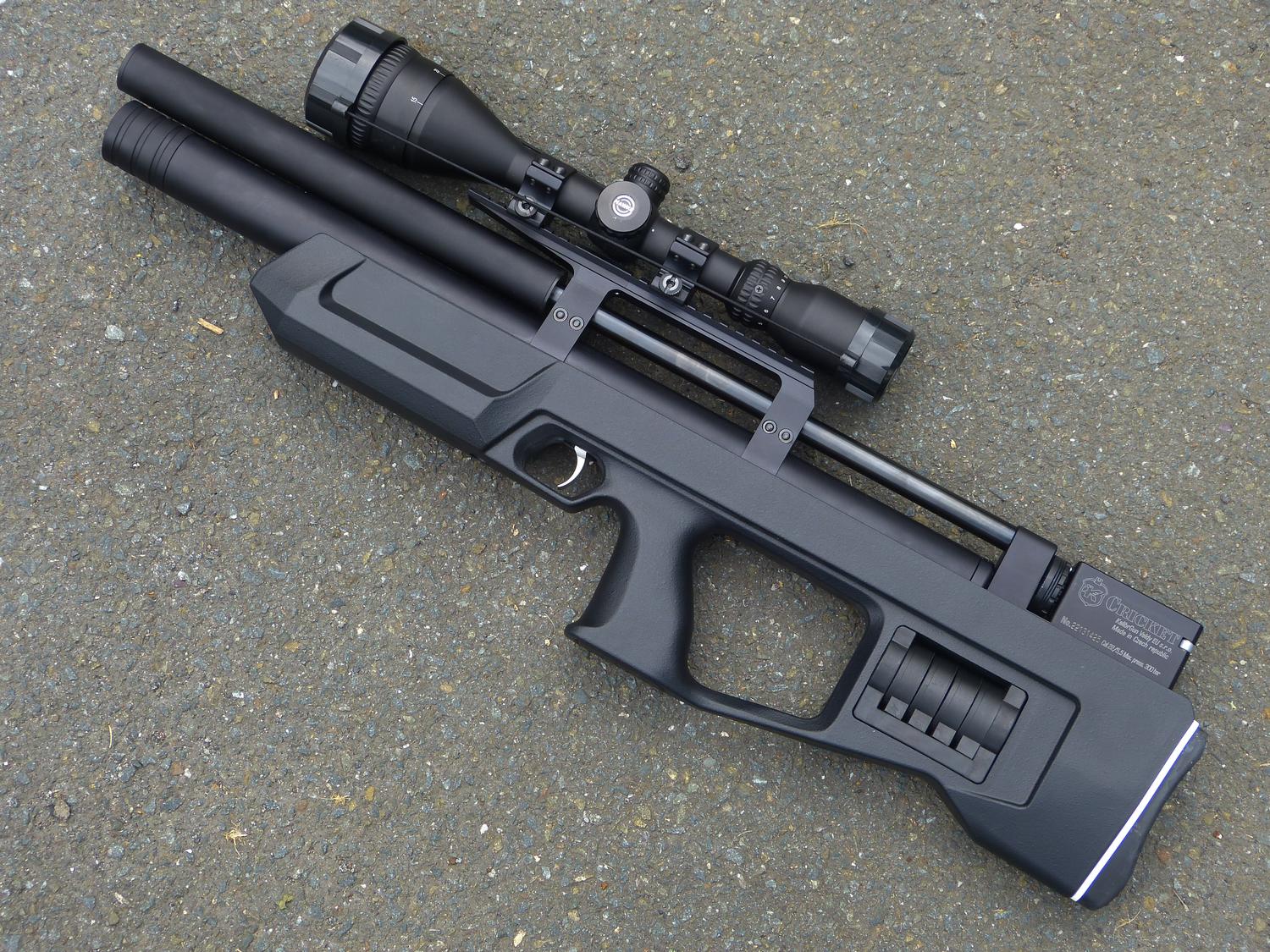
Many problems can bother you while installing airguns. Most manufacturers do not think or have a clue about how their clients will be using a gun. Some use many different screws instead of one size screw all around during installation.
The following are the best engineering practices while designing airguns so that you cannot make mistakes that you can avoid.
Using fasteners of equal size whenever feasible
Fasteners that are equal and common in size are the best because they help reduce the number of tools required for working as well as simplify the supply chain. Common size fasteners are the size of the device that is needed to tighten the gun, thread pitch and the diameter of the shank. The length of the fastener depends on the application but is vital to keep standard always.
- Take time in designing various gun platforms so that you can adapt to as many uses as possible.
Time spent doing research is significant because it can pay you colossal dividends. When you design carefully, you will reduce additional work in the installation of other successive airguns. If you are developing one shot, it is essential for you to spend much time on it to avoid repeating the same action later on.
- Do not add other features that the shooter may not require
Air rifle technology is not advancing rapidly, however, always learn to offer something different in the market. This means that it does not matter what the clients need, provide an extra feature so that the package of the airguns can become longer. The typical feature is the scope sights that enable you to see through the open slights even if the gun is mounted. Many shooters do not understand that, but it is essential to add it.
- Use materials that are designed specifically for the application
Do not only choose a material that meets its performance requirement but also one that exceeds its application. The air rifle technology allows you to use the seal not only because that is new and fresh but also one it can last for a long time when put under operation. For example, a seal with a small durometer can work well when it is new, but over time it may work incorrectly due to its softness. The practice should work in the real world, and that is why it is essential to make it practical.
Learn to design in a modular way
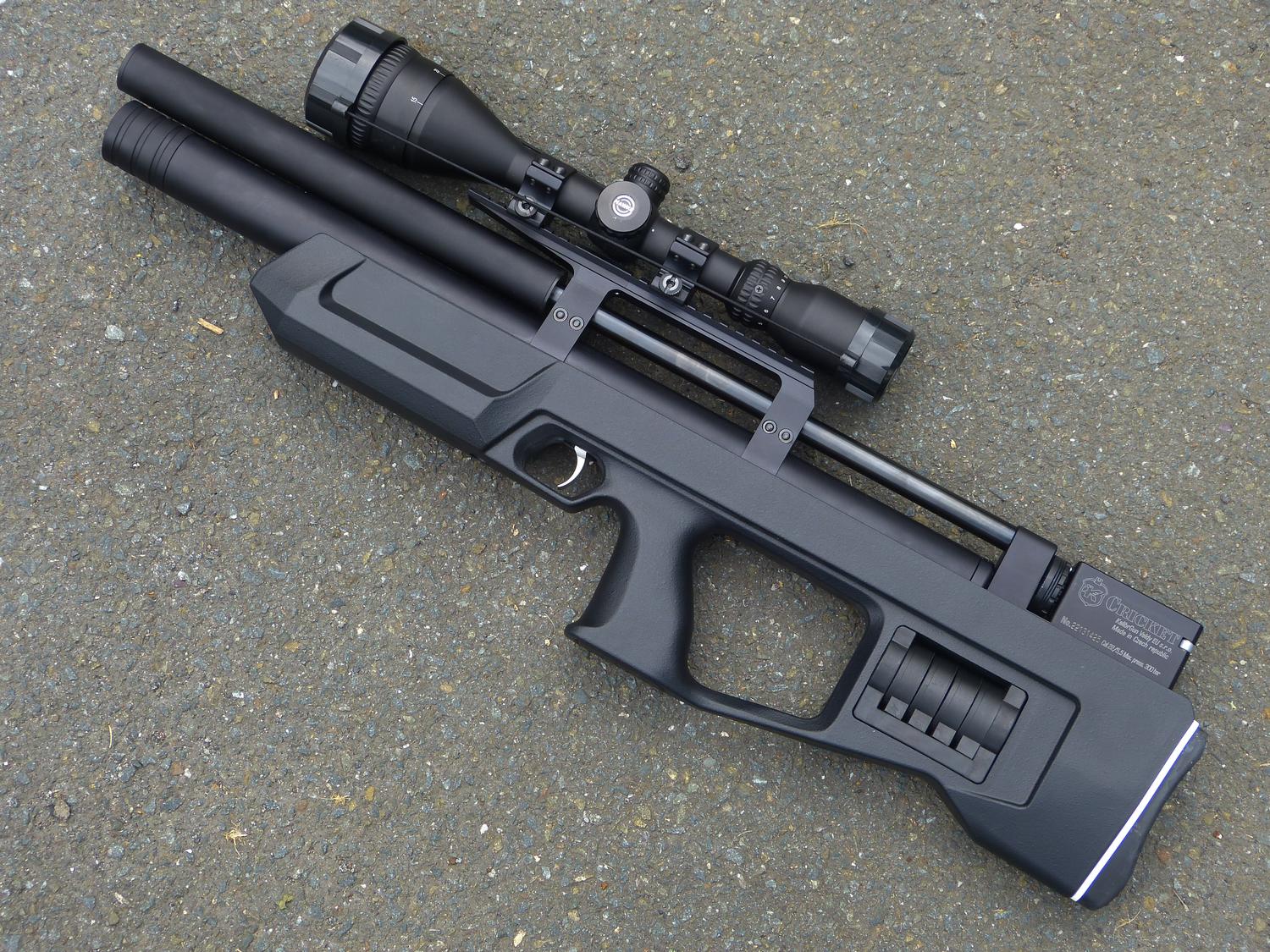
Ensure that the trigger has all parts contained in one unit that you can handle outside the airgun without losing other parts. Additionally, make sure that the power plant can be disassembled effortlessly without the need to hold jigs or fixtures.
Let the marketing and designing team test the airgun before you release it to the market
Many airguns in the market do not work because they never undergo testing. It is wise to examine it so that it cannot fall apart within a short time or become challenging to droop when using the scope.