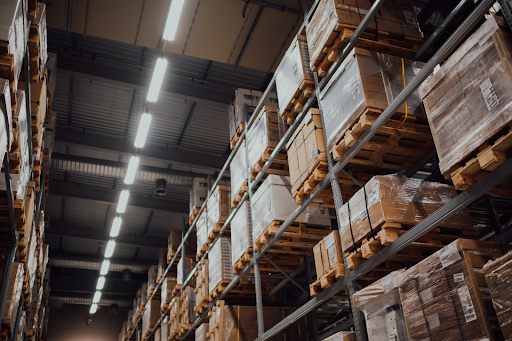
When embarking on a new project, whether it's a construction job, a manufacturing operation, or even a simple office renovation, procuring the right equipment and supplies is crucial for its success.
However, the process of acquiring these essentials involves more than just placing orders - you need to deal with multiple hurdles before you get the equipment you need, right from buying quality materials that are affordable to transferring these materials to the place of the project.
To ensure a smooth and efficient project, you need to pay close attention to various logistics aspects. In this blog, we'll explore eight important logistics considerations when buying new equipment and supplies for your project.
1. Assess Your Project Needs
Before you even start shopping for equipment and supplies, it's essential to have a clear understanding of your project's requirements . What specific tools, machinery, or materials will you need? What quantities are necessary? Create a detailed list to avoid over or under-purchasing, as both can lead to unnecessary costs and delays.
2. Budget Management
Budgeting is a critical aspect of procurement logistics. Establish a realistic budget for acquiring equipment and supplies, including not only their purchase costs but also any associated expenses, such as shipping, taxes, and maintenance. Sticking to your budget will help you avoid financial surprises down the road.
3. Supplier Selection
Choosing the right suppliers is pivotal to the success of your project. Research and evaluate potential suppliers based on their reputation, reliability, quality of products, pricing, and proximity to your project site. Establishing strong partnerships with dependable suppliers can help you secure better deals and ensure timely deliveries.
4. Delivery Scheduling
Timely delivery of equipment and supplies is essential to keep your project on track. Coordinate with suppliers to establish a clear delivery schedule that aligns with your project timeline. Be sure to account for any lead times, potential delays, or seasonal variations in supply chains.
5. Logistics Management
Effective logistics management is the backbone of a successful procurement process. Consider how the equipment and supplies will be transported to your project site. Will you need specialized transportation for oversized machinery? Are there any regulatory requirements or permits needed for transportation? Addressing these questions in advance can prevent transportation-related setbacks.
In fact, it may be wise to try using a route planner as this will help you find the shortest and quickest route from one store to another - making the entire process more smooth and efficient.
6. Storage and Inventory Management
Once your equipment and supplies arrive, you'll need a suitable storage solution. Proper inventory management is crucial to prevent theft, damage, or misplacement of valuable assets. Implement a tracking system to monitor your inventory levels and ensure that you have what you need when you need it.
7. Quality Control and Inspections
Before putting new equipment into operation or using supplies for your project, conduct thorough quality control checks and inspections. Ensure that everything meets the required safety and performance standards. This step helps prevent accidents, equipment failures, and costly rework down the line.
8. Maintenance and Support
Don't forget about the ongoing maintenance and support requirements for your equipment. Many projects rely on machinery that needs regular servicing and repairs. Establish maintenance schedules and access to support services to minimize downtime and keep your project running smoothly.
In addition to these eight logistics considerations, it's worth noting that communication and collaboration are key throughout the procurement process. Effective communication with suppliers, project teams, and stakeholders can help mitigate potential issues and ensure everyone is on the same page.