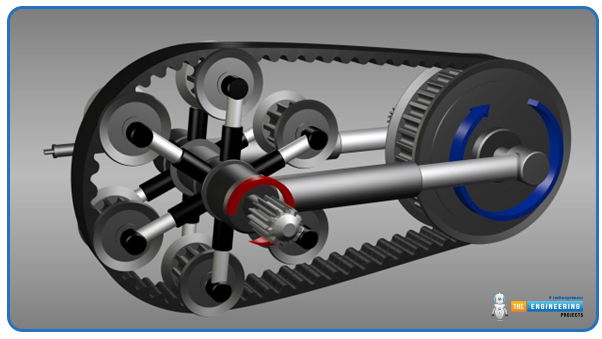
Hi readers! Hopefully, you are doing well and exploring something new. Every powerful machine has a secret weapon, a machine that few think about but is responsible for all speed, torque, and, relatively speaking, performance. That secret weapon is an incredibly engineered gearbox. Today, we discuss gearbox design.
Gearbox design and selection are amongst the most critical elements of mechanical engineering, as they involve how power will be best transferred between two rotating shafts. A gearbox changes speed and torque position from a power supply (usually a motor) to the required application. Gearboxes accomplish this through a series of different types of gears, in various configurations. Gearboxes allow machines to perform under various parasitic load conditions.
Gearboxes vary widely, from automotive experiences with gearboxes or transmissions, industrial equipment, wind turbines, and robotics. Each of these applications will have vastly different required gear configurations: spur gears, helical, bevel, worm or planetary gears. The selection of gears will vary due to the constraints of required gear ratio, torque, noise level, or efficient size in the application and lastly, the level of environment needed for the gearbox to be optimally integrated.
Designing a gearbox includes a number of considerations such as: material of the selected gears, efficiency, lubrication, heat dissipation, and the expected life span of the gearbox components. Key considerations of a gearbox design include gears, shafts, bearings, housing and controls. Careful consideration must be made so that losses in power can be minimised and that reliable operations are guaranteed with a long operational lifespan, with stresses that may be encountered in different environments.
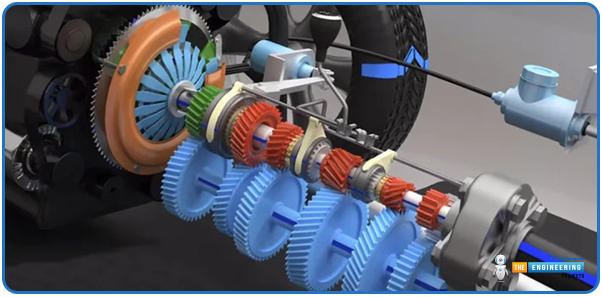
Here, you will find the definition of the gearbox, its basic parts, types of gears used in it, types of gearboxes, objectives in gearbox design, steps to design a gearbox, and applications. Let’s unlock detailed guidance.
What is a Gearbox?
A gearbox takes power from an engine and sends it to another device, changing both speed and torque. A gearbox supplies the right RPM and torque levels for different types of vehicles and equipment. A gearbox changes speed and torque by % using different ratios. Gearboxes provide an efficient means of changing motion and torque, better overall performance, and improved fuel consumption. Gearboxes are found in many mechanical systems such as vehicles, industrial machines, and wind turbines.
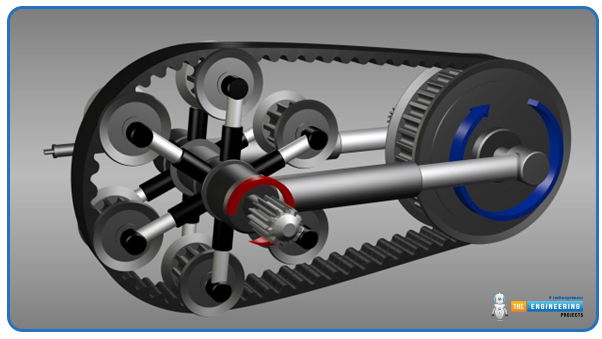
Basic Parts of a Gearbox:
Examining the pieces in a gearbox helps the designer and maintainer work on and troubleshoot problems with it. Every component is necessary for transferring power efficiently, without much wear on the machine itself. The basic parts of a gearbox are as follows:
1. Gears:
Gears are the main component of a gearbox that change speed and torque. Gears transmit motion by engaging in pairs to convert the rotary motion of one shaft to another shaft with a designed gear ratio.
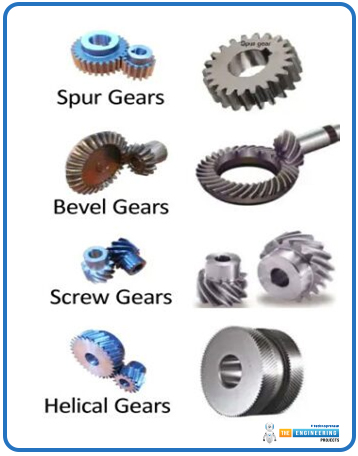
Gears Types:
Spur Gears: connect parallel shafts, and are also one of the simpler ways to transmit power and motion.
Helical Gears: have angled teeth that allow for smooth, quiet operation.
Bevel Gears: used for shafts at right angles.
Worm Gears: best used for high rates of torque reduction, and are best for a compact design.
Depending on the function required by speed, load, and spatial limitations, each gear type equally serves a purpose. Design considerations will consider material strength, tooth geometry, and precision machining to achieve the best contact point with minimal backlash.
2. Shafts, Transmit Rotary Motion:
Shafts are the mechanical axis by which gears will turn, allowing for the transfer of torque and motion to other mechanical devices.
Shaft Types:
Input Shaft: the shaft that connects the source of power (e.g., engine, motor).
Countershaft: intermediate shaft that utilises gears but does not provide any motion; it is used to distribute torque.
Output Shaft: provides adjusted torque and speed to the driven mechanical device.
For the most part, shafts are made from alloy steel, and they must be engineered to support constant and changing forces that could cause them to bend, twist and weaken. It is extremely important to make sure all rotating parts are aligned and balanced, because misaligned or unbalanced parts can eventually damage the machine.
3. Bearings, Reduce Friction and Support Loads:
Bearings make possible the smooth and stable rotation of the shafts and minimize friction between moving pieces. Bearings assist in supporting both radial and axial loads, and specific gearbox designs may be used for specific applications.
Common Bearing Types:
Ball Bearings: Suitable for any light radial and axial loading.
Roller Bearings: Suitably rated for a heavy radial loading.
Tapered Bearings: Suitable for a combination of radial and axial loads.
Bearings will last indefinitely anything by protected from contamination and kept lubricated.
4. Housing - Structure, protection:
The housing provides the outside structure to the gearbox; it houses the internal components, provides structural support, and corrosion, allowing gears and shafts to be properly aligned.
The housing does the following:
Protect gears and bearings from dirt, debris, and moisture.
Act as a reservoir for lubricants.
Dissipate heat generated from mechanical operations.
Minimise the noise and vibration of operation.
Commonly used materials are cast iron for heavy-duty applications, and aluminium for lightweight machinery - it is essential that the housing be machined to an accuracy to stay within tolerances, and hold gears and shafts in position without misalignment.
5. Lubrication System - Reducing wear; Cooling:
Lubrication is critical for effective operation and longevity of components. Reducing friction, transferring heat, and preventing metal-on-metal contact is the lubricant's job.
The methods of lubrication are:
Splash Lubrication: A simple method, and one most used; gears dip into an oil bath.
Forced Lubrication: Pumps provide oil right to critical parts.
Mist Lubrication: Uses very fine oil mist, used for all high-speed gearboxes or other applications.
Types of Gears Used in Gearboxes:
Different types of gears are used in gearboxes based on specific design parameters such as the required torque being transmitted, physical constraints such as available space, and noise and speed variation control parameters. Below is a list of the most common gears.
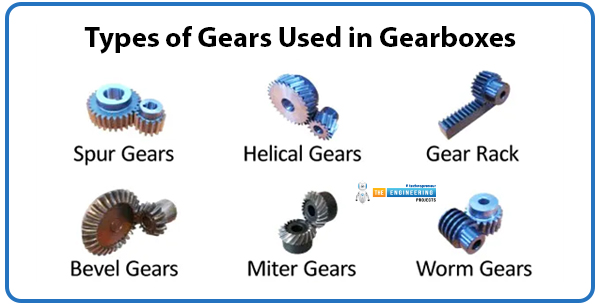
1. Spur Gears:
Spur gears have their teeth cut straight and are assembled on parallel shafts. The design is simple, it is easily produced, and it is very efficient. The drawback to spur gears is that they typically create the highest amount of noise and vibration, especially when run at higher speeds.
2. Helical Gears:
Helical gears have angled gears which engage gradually in a more controlled manner, which results in less noise and vibration and a smoother operation. Helical gears can be used to transmit higher loads, but introduce axial thrust, which should be accounted for. They are popular for high-speed or heavy-duty applications
3. Bevel Gears:
These days, bevel gears are commonly built for shafts that connect at a 90° angle. Because bevel gears are built as cones, they permit the direction of power delivery to change. Bevel gears are commonly integrated into differential drives and gearboxes that form right angles.
4. Worm Gears:
They are made up of a worm (the screw) with a worm wheel. They can produce strong torque in small packages and are applied at high-speed reduction rates. Sliding contact in worm gears makes them less efficient and likely to produce heat.
5. Planetary Gears:
The parts of a two-stage gear system are a sun gear, several orbiting planet gears and an outer ring gear. Because planetary gears have a high ratio of power to space, they are usually selected for use in many automotive, robotics and aerospace machines.
Types of Gearboxes:
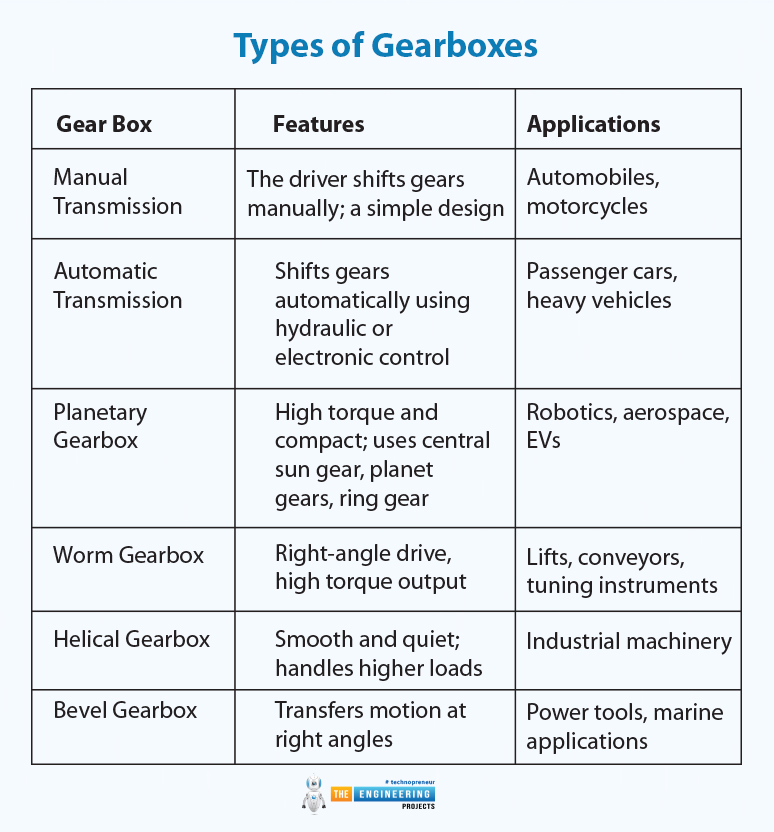
Gear Box |
Features |
Applications |
Manual Transmission |
The driver shifts gears manually; a simple design |
Automobiles, motorcycles |
Automatic Transmission |
Shifts gears automatically using hydraulic or electronic control |
Passenger cars, heavy vehicles |
Planetary Gearbox |
High torque and compact; uses central sun gear, planet gears, ring gear |
Robotics, aerospace, EVs |
Worm Gearbox |
Right-angle drive, high torque output |
Lifts, conveyors, tuning instruments |
Helical Gearbox |
Smooth and quiet; handles higher loads |
Industrial machinery |
Bevel Gearbox |
Transfers motion at right angles |
Power tools, marine applications |
Objectives in Gearbox Design:
The core goal of gearbox design is to create an optimal system performance, reliability, cost, and operational efficiency. A good gearbox will provide an efficient means of transferring power to the driven machines while also tolerating in-use rigours and tribulations. Below are the key objectives in gearbox design:
1. Power Transmission:
The primary aim of any gearbox is to transmit power from the driving source, such as a walking beam pump or other motor devices, to the driven machinery as efficiently as possible. The proper torque and speed are needed for any given application. The designer must select the proper gear ratios, confirm or make the best provisions for the gearbox to accommodate the expected loads and provide leeway not to experience slippage or power loss while operating and without mechanical collapse.
2. Durability & Reliability:
In many applications, gearboxes are used for long periods and frequently in harsh environments. Gearboxes will need to be able to withstand wear, fatigue, thermal cycling and many other considerations over their entire service life. Choices in material selection, surface treatments, alignment, load distribution and reduced stress must be made to reduce failure rates.
3. Size and Weight Reduction:
Many applications, particularly in automotive, aerospace, and robotics, have strict size and weight restrictions. The gearbox must be designed to be as compact and light as possible, avoiding loss in strength or performance. This invokes a lot of thought into gear configuration and the housing that provides maximum power density.
4. Noise and Vibration:
Modern gearbox design incorporates reducing noise and vibration during operation, especially in consumer or comfort-sensitive locations. This has been done with components such as helical gears, precision machining, and the use of noise-reducing materials. A quieter gearbox usually means smoother mechanical operation and will experience less wear over time.
5. Thermal Management:
Gearboxes produce heat due to friction between moving parts. Effective design calls for adequate thermal management, from sufficient lubrication to heat dispersal in the gearbox housing, or even cooling systems. For component and performance efficiency in the long run, gearboxes should operate at sufficient and consistent temperature ranges.
Design Process for a Gearbox:
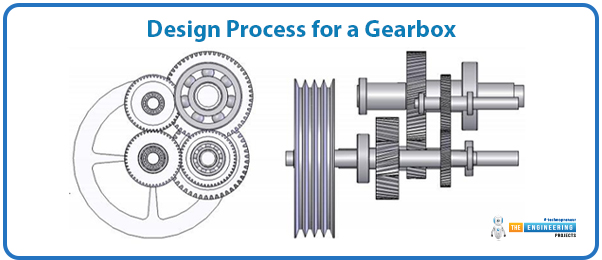
Step 1: Determine Requirements
The design begins with determining requirements around the application, such as input and output speed, torque quantities, and conditions of the application, such as ambient temperature, load cycles, or even environmental exposure. These requirements must be noted down as they will guide every decision that follows.
Step 2: Select Gears
Designers consider the style of gear (spur, helical, bevel, etc.), but also the demands form the application. An important consideration will be material, considering strength and wear resistance. The designer has to calculate the specific gear ratio, consistent with speed and torque.
Step 3: Design Shafts and Bearings
Shafts must be designed considering torsional resistance and bending resistance, while bearings take into consideration radial and axial loading. It is imperative to will also keep shafts aligned to ensure a service life without premature failure.
Step 4: Housing and Layout
The house requires sufficient support for all internal components and contains sufficient provision for lubrication, cooling and maintenance. Structural rigidity and precision of internal layout are critical factors.
Step 5: Lubrication and Cooling
Selecting the right lubricant and delivery method will ensure a loss of friction and squash continued operation. Designing provisions for heat dissipation can be equally as important as avoiding thermal degradation.
Step 6: Conduct safety checks and durability tests
The designer will conduct the final step on their design with fatigue check, checks for overload, and cap it with Finite Element Analysis (FEA). If prototypes are fabricated, they can also be subjected to real-world tests to validate that the design as-built meets their expectations and still meets their design objectives under conditions of use.
Applications of Gearboxes:
Automotive:
In the automotive world, gearboxes are found to be critical in both manual and automatic transmissions, and electric vehicle (EV) drive units, ensuring effective power delivery and optimization of the available fuel or battery energy.
Industrial Machinery:
In industrial machinery, gearboxes are present in conveyor systems, packaging/inspection machines, and material handling equipment, which provide the ability to modulate motor output to operational speed and torque requirements.
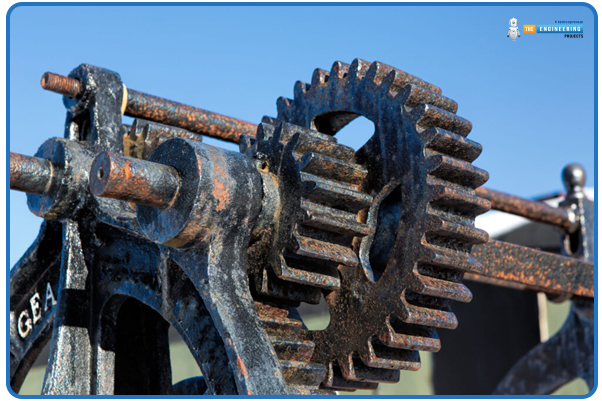
Aerospace:
In aerospace, gearboxes are present in helicopter main and tail rotor drives (or engines) and in the position mechanism of satellites. These have a requirement for high precision and reliability to operate in harsh environments.
Wind Energy:
Gearboxes in wind turbine applications would be responsible for increasing the slow rotational speed of the rotor to a higher speed that is used by the generator, which improves the throughput of electric power production.
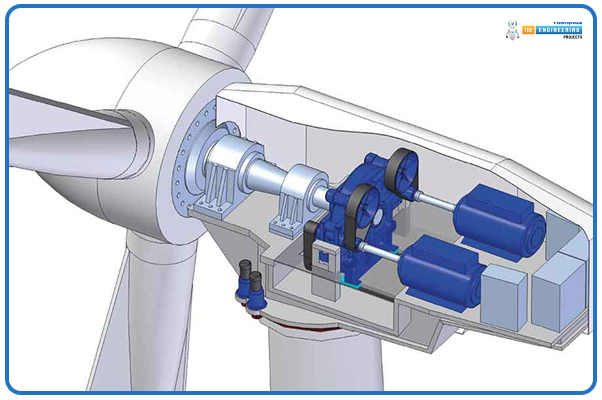
Marine:
In marine applications, gearboxes can assist in directional propeller drives, anchor winches and thrusters, which all have requirements to withstand extreme loads and corrosion.
Robotics:
When a robot moves, gearboxes will typically be used to match the human-like control of joint movement with high accuracy and repeatability, especially in robotic arms and automated manufacturing systems.
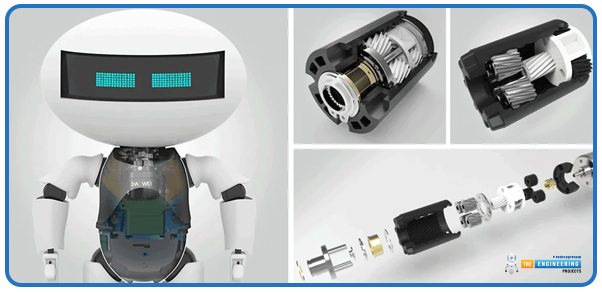
Conclusion:
Gearbox design is a vital part of modern mechanical engineering, making power transmission systems work. From automobiles to industrial applications, in aerospace, robotics, and renewable energy, gearboxes provide regulated, efficient torque and speed transmission. Moving from concept to reality, gearbox design starts a complex process that takes into account gear type, shaft geometry and alignment, bearing loads, gearbox housing structure, component lubrication, and thermal management.
A careful balance of durability against performance, size, cost, and noise is paramount. Modern gearbox design combines advanced materials and manufacturing techniques with computer-aided design (CAD), simulation technologies like finite element analysis (FEA), and successful design ideas have led to compact, reliable, and energy-efficient gearboxes. Industry is demanding compact size with more performance, so gearbox design will continue to innovate, integrate, and develop precision power for the foreseeable future. Because gearboxes need to be more compact and have more performance, they will need to be socially responsible while reducing the total cost of ownership. Gearboxes must continue to deliver, better and better, so our world can be powered with the most efficient designs with reliability built in.