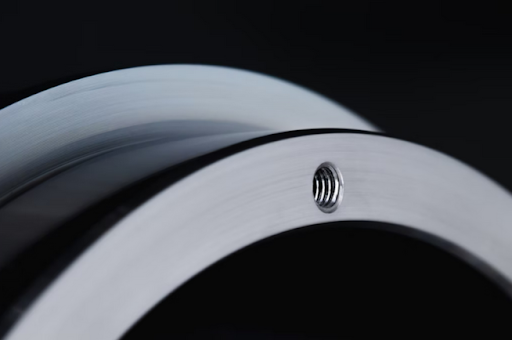
Several manufacturing processes for plastic manufacturers and metalworkers, like milling or casting, produce burrs. However, to guarantee the safety and quality of a component, one needs to ensure smooth edges that will not cause any problems in further processing or use of the item. Deburring and brushing machines are solutions to this issue.
High-quality deburring technology from Germany can be integrated into casting and cutting machines, and to automatically produce flawless components.
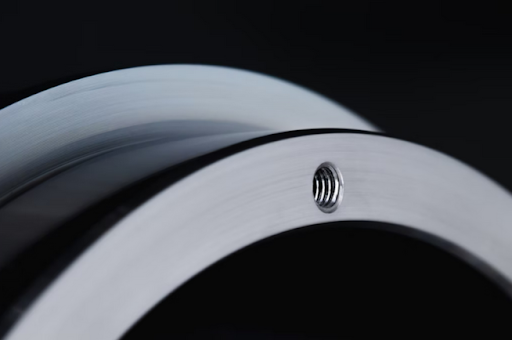
What are Burs, and How do They Develop?
Burrs are unwanted protrusions of a material like metal or resin that can develop during processing.
When picturing a component like a gear, it is easy to understand, that any kind of imperfection can cause serious problems for the machine the gear is used for. Here, we need to make sure it can rotate easily and will not grate and damage other machine parts.
For the safety of other products, assembly processes, and operators, we need to eliminate these imperfections and protrusions.
Where do Burrs Develop?
There are several materials and processes that can cause burrs to appear. This mostly applies to steel producers and metalworkers , as well as plastic manufacturers.
Burrs develop during:
Super Finishing,
Honing,
Grinding,
Broaching,
Milling,
Turning,
Boring,
Drilling,
Metal Sawing,
Pressing,
File Finishing,
Forging,
Casting,
Welding, and
Fusing.
For materials like:
Stainless Steel,
Steel,
Special Alloys,
Copper,
Brass,
Aluminum,
Sinter Metals, and
Synthetic Materials, like Plastic and Resin.
How to Remove Burrs
Multiple machines can help remove burrs; from small manual applications for low quantities to fully automated AI-driven deburring machines integrated into serial production.
The German-based company Loeser has used its over 80 years of experience to become the standard for automated deburring with over 500 installations worldwide. Their top-of-the-line automated deburring centers can be linked to computer-controlled wheel handling conveyors to enable a 20 % production increase.
The Deburring Process
Deburring machines can use several methods to create flawless components. Typically, the process has two to three steps:
Removing the Primary Burrs – This removes the protrusions that have been created during processing, for example with grinding.
Removing the Secondary Burrs – The grinding process can create secondary burs. With scotch brushes and abrasive brushing techniques, the workpiece’s original geometry can be restored, this time burr-free.
Rounding of Edges – This step is optional. The component now no longer has burrs, but still has sharp edges. If required, to reduce the risk of injury when handling the parts, a deburring machine can also round any edges.
Deburring Methods
There are different kinds of deburring machines and techniques. In general, the machine must be tailored to the individual industry processes and resulting items. Some types of component shapes and materials are better off with a specific deburring method than others.
A professional manufacturer of deburring machines like Loeser will help their clients find the ideal solution for their needs.
Deburring can be achieved via:
Manual Deburring
Manual deburring machines are small hand tools with curved or hooked sharp edges you can use to cut away burrs.
Punch Deburring
For punch deburring, you use a punch machine with a mold fitted to cut away the burrs of the created component. This technique is more efficient than manual deburring but does not allow complex shapes.
Tumbling
With the tumbling technique, parts are put in a rotating barrel along with water, compounding agents, and an abrasive media. Burrs get removed with the friction. The result is very fast and cost-efficient, but not very precise.
Grinding and Rolling
Like the tumbling technique, here, the components are subjected to a rotating wheel made from abrasive materials that remove protrusions on contact.
Thermal Deburring
In thermal deburring, the burrs are removed by igniting a mixture of gas surrounding the components in a deburring chamber. This process is very fast but requires further processing such as surface treatments like pickling. Here, we also need to pay special attention to the correct mixture of the used gasses.
Electrochemical Deburring
In electrochemical deburring, the deburring tool is an anodic metal dissolution with cathodes that dissolves the burrs. This technique is typically used to deburr hard-to-reach and very small areas.
Hole Deburring
During the hole deburring method, a spring-loaded cutting tool removes the burrs that have developed inside a hole, like the inside of a pipe. The component must be positioned very precisely for the cutting tool to go through the hole smoothly.
Brush Deburring
Brush deburring is a very cost-effective and fast method that can be used on complex shapes. Here, the components are deburred with brush tools, which may contain abrasive substances. Similar to using sandpaper manually, the machines can fit themselves into several shapes and create smooth and rounded edges. This is the most used technique for automated burring machines integrated into processing lines.
Conclusion
Deburring is a necessary process to remove unwanted accumulations of metal or other materials that can develop during various processing methods. Deburring machines remove the protrusions to guarantee safe handling and further processing of the components.
Automated deburring machines with brushes can be used to gain smooth-finished pieces right from the processing line. The German company Loeser has established itself as the leading manufacturer of efficient deburring processes, which can raise productivity by as much as 20 %.