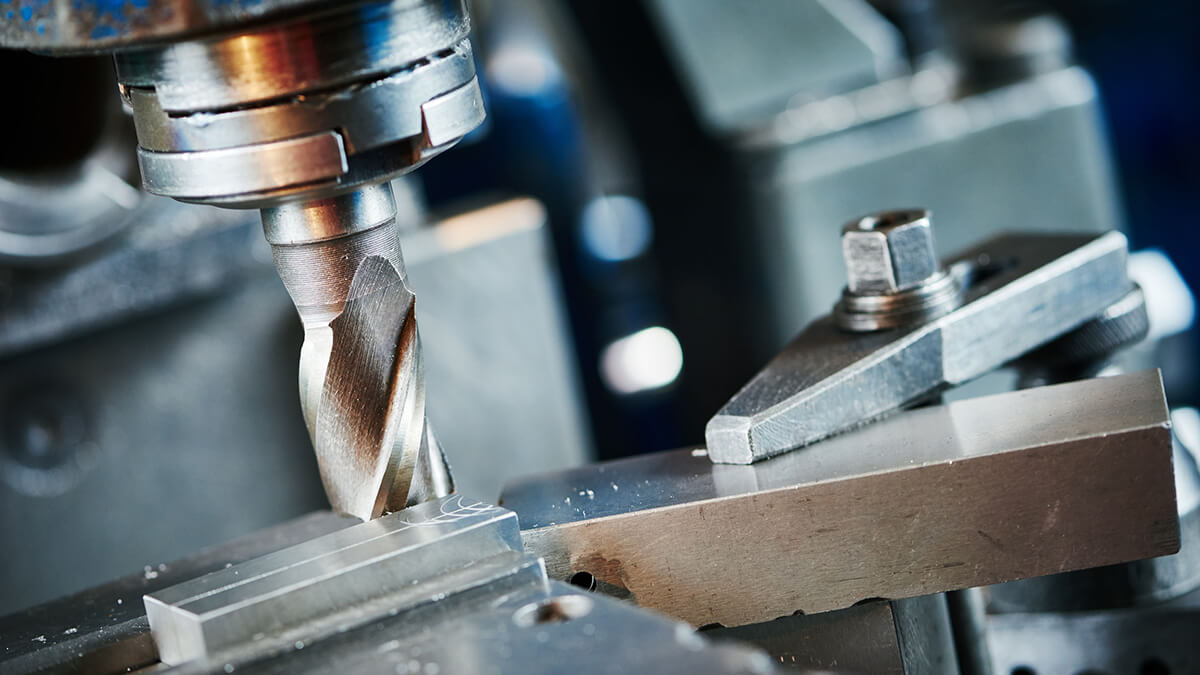
Milling machines are the backbone of any workshop, whether you're crafting aerospace parts or tuning up motorcycle brackets. With the sheer range of options out there, it’s easy to get lost in the noise.
Still, you must understand that choosing the right milling machine is a crucial investment that must be done carefully. The machine determines your precision, productivity, and long-term shop performance.
Your project needs, material type, and budget all shape the right fit. Key factors include the machine type (CNC, manual, vertical, or horizontal), spindle power, and available workspace.
This guide breaks down the fundamentals to help machinists, hobbyists, and production operators make confident decisions based on real needs.
Understand Your Milling Needs
Start with the materials. Cutting aluminum is a different game than chewing through hardened steel.
Softer metals need less torque and allow faster feeds. Steel or titanium requires more horsepower and a rigid build. Wood and plastics bring lighter cuts, but very different RPM ranges.
Now think scale. Are you machining small precision components or bulky brackets? Tight-tolerance work calls for high-quality leadscrews and fine-resolution DROs. Larger parts demand a heavier table, more Z-axis travel, and stronger motors to match.
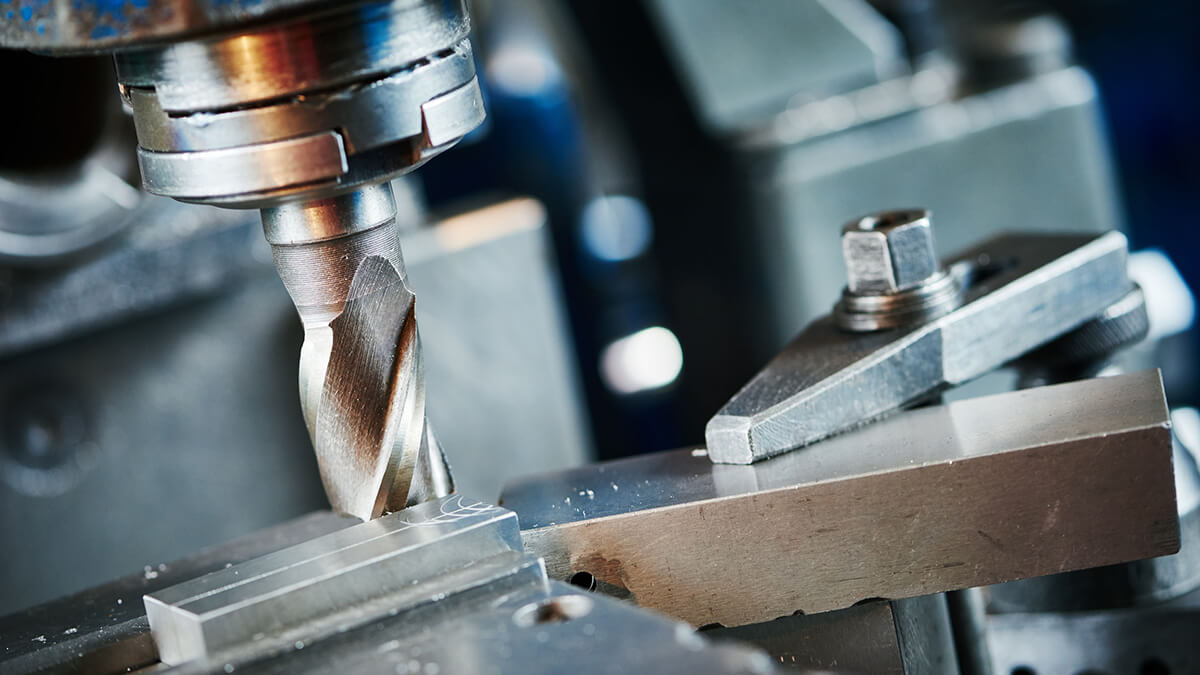
Your skill level and usage frequency matter too. If you’re learning, a manual mill helps build essential feel and technique. For repeat production, CNC milling machines save both time and scrap.
Be honest about how often you’ll run it. Overbuying a machine that sits idle most of the week only burns budget.
Key Types of Milling Machines
Milling machines come in several types, each built for a specific purpose. And while this guide focuses on metalworking mills, it’s worth noting that there are specialized milling machines like basket mill that are used in industries like paints, coatings, and cosmetics for fine wet milling and dispersion work.
That said, picking the right milling machine depends on your materials, part design, and output volume.
Check this out:
Vertical mills: The spindle moves vertically. These are great for face milling, plunge cutting, and general machining. They’re also ideal for prototypes and light production work.
Horizontal mills: The spindle sits horizontally. These machines shine when it comes to deep cuts and heavy stock removal. A solid choice for production environments or large workpieces.
CNC mills: Software-controlled machines known for precision and repeatability. Best suited for complex geometries and high-volume jobs where tolerances are tight.
When in doubt, look at your most common jobs. Don’t buy a horizontal mill if 90% of your work is small flat plates. And if you’re eyeing future projects, make sure the machine you pick won’t box you in.
Budget and Brand Considerations
Start by defining your budget.
Manual mills often begin at around $3,000, while CNC machines typically start at $15,000. Tooling and accessories, like vises, collets, or coolant systems, can add 20–30% to the total cost.
Stick with reputable brands. Companies like Bridgeport, Haas, Tormach, and Laguna have earned trust for a reason. They offer better tolerances, dependable tech support, and decent resale value.
When researching, check machinist forums or YouTube reviews. If a brand has a loyal following, there’s probably a good reason.
The other thing to think about is new vs used machines. New machines come with warranties and modern features. Used machines can save thousands, but they need a sharp eye. Check backlash, listen for spindle noise, and inspect ways for wear.
Certified refurbished equipment often strikes the best balance for beginners: lower price, solid performance, and peace of mind.
Essential Features to Consider
The machine type matters, but the features determine performance. These are the specs that directly affect precision, usability, and lifespan.
Spindle power & speed: Most shops do fine with 1 to 5 HP and an RPM range from 500 to 5,000. Pay attention to torque, not just peak horsepower. Cutting stainless steel at 2,000 RPM needs more torque than cutting plastic at 5,000 RPM.
Table size & axis travel: A 30" x 12" table offers solid versatility. Aim for at least 16 inches of Z-axis travel to ensure tool clearance and accommodate taller setups.
Controls: A digital readout (DRO) system should be standard. If you're even slightly considering CNC down the road, make sure your control system is upgrade-friendly. Manual now, automated later is a common path.
Pro tip: Compare usable travel, not just listed table size. A big table doesn’t help if only half of it is accessible with the tool head.
Safety and Maintenance Tips
Treat your machine right and it’ll serve you for years. Here’s how to stay safe and keep things running smoothly:
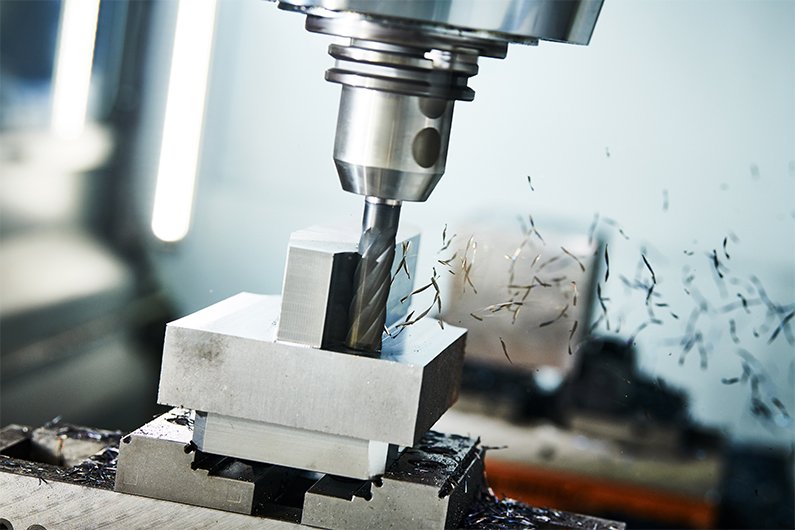
Always wear eye protection, gloves, and hearing protection.
Keep clothing, sleeves, and jewelry well away from spinning parts.
Clean the machine after each session. Chips collect fast and can cause wear.
Follow the lubrication schedule. Don’t just lube when the ways start squeaking.
Replace worn tooling early. A dull cutter does more harm than good.
Follow those safety tips to keep yourself safe and ensure the machine serves you over the long haul. And remember, the emergency stop button is for emergencies, not bad planning.
Conclusion
Choosing a milling machine doesn’t have to be overwhelming. With a clear understanding of your material types, part sizes, and production goals, you can narrow down your choices and find a machine that suits your workflow.
Buy with growth in mind. Stick with known brands, invest in quality features, and don’t cut corners on safety. The right machine will boost your efficiency, improve your results, and make machining more enjoyable over time.
Happy machining.